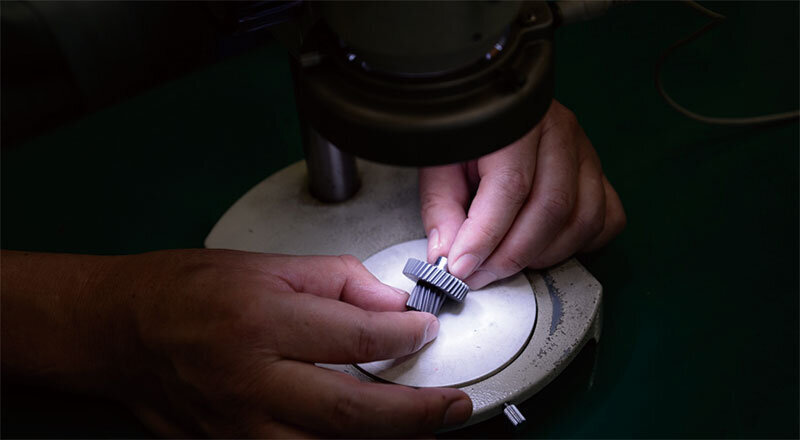
目次
- 特殊な小歯車減速機の製造が主力。多岐にわたる設備の保有と設計から加工・組付までワンストップで対応できることが強み
- 原材料費高騰でも値下げを迫られ、設計料すらもらえないことも多い。多岐にわたる設備を生かし、企画段階から関わりたい
- AIカメラを備えた検査機器を導入し、時間を要する検査工程を短縮・省力化して人的リソースを組立にまわす計画
- 3D-CADを導入すれば歯車の噛み合わせがシミュレーションできる。取引先とのデータのやり取りにも円滑に応じたい
- 生産設備のIoT化を実現すれば設計データが迅速に反映できる。事務所と工場で社員が情報共有できる生産管理体制の構築へ
- 大手にはできないものづくり技術で貢献し、新たな付加価値を創出。人間にしかできない部分を生かしてDXへつなげていく
産経ニュース エディトリアルチーム
高級絹織物「桐生織」の産地として知られる群馬県桐生市。「織都」とも称される桐生は古くから絹織物産業で栄え、「西の西陣、東の桐生」と称賛されてきた。産地としての特徴は明治期に他の産地にさきがけて工場制手工業を取り入れてきたことだ。そして、水車の動力を利用した力織機(機械織機)や、桐生織の「お召し」に欠かせない撚糸を作る八丁撚糸機、柄織りのプログラミングを担うピアノマシンなど、精緻な機械織の技術開発や多品種少量生産を強みに産地として成長してきた。しかし、円高経済への移行に伴い世界市場での競争力を失い、さらに労働力の安い中国からの輸入によって日本国内の繊維産業は衰退していった。桐生でも廃業した織物製造業は数多い。とはいえ、桐生は他の繊維業の産地とは少々異なる側面がみられる。それは、多品種少量生産という強みを生かして時代に即した製品開発と設備投資を行い、経営を堅持する企業も少なからず存在していることだ。
今回の事例は桐生で小型歯車減速機の設計・製造・組立を手掛ける有限会社根本製作所という小規模の製造業だ。かつて桐生には機械織機に使われる金属部品の製造を担う零細工場が数多く存在し、そうした経歴を持つ工場が今では自動車部品などを作っている。しかし、金属工業も繊維産業と同様にコスト面で安価な海外生産品にはかなわず、苦しい状況が続いている。ただ、注目したいのは、同社が先述の織物産業と分野は異なるものの、保有するリソースが相似していることだ。それは、設備投資を行いながら多品種少量生産を手がけ、取引先の要請に柔軟に対応してきた生産力と創造力。そしてもう一つは高い技術力だ。
今、このような小規模の製造業が保有するリソースを生かし、生き残っていくためにIoTとICTは不可欠だ。ICTの導入によって、これまで属人化されていた業務や手間のかかる作業を省力化すれば、人的リソースを有効活用して新たな付加価値を創出し、競争力を高めることも期待できる。さらに大手メーカーとの取引においては、特定の規格に準拠した生産管理体制に応じていくことも求められ、生産規模に関わらずIoTとICTは避けては通れない。
桐生に根ざす「ものづくり魂」を受け継ぐ同社はまさに今、IoTとICTによって自社の強みをさらに引き出し、強い競争力を持つ製造業への転換を目指している。多様性が新たな付加価値を生む小規模製造業の可能性を追った。(TOP写真:加工後の歯車の凹部に傷がないか、顕微鏡で厳しい最終チェックが行われる検品工程)
特殊な小歯車減速機の製造が主力。多岐にわたる設備の保有と設計から加工・組付までワンストップで対応できることが強み
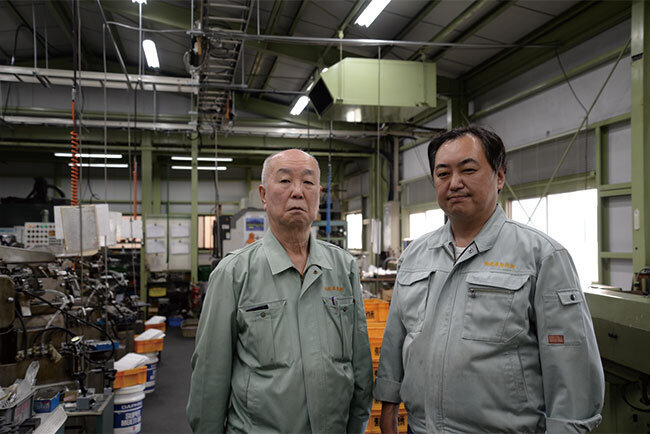
「たいていのものには対応できます。この筺体(モーターや歯車などの機構を収めるケース)の中にこんなものが欲しい、とラフなスケッチで頼まれることもありました」。と話すのは、桐生市で小型歯車減速機の製造を手がける有限会社根本製作所の代表取締役根本健一氏。筺体のサイズと求める荷重のオーダーに応じて設計を行うものの、それがどのような最終製品に使われるのか、知らされない場合がほとんどだという。「私たちは何に使われているのか知らないんですよ。でもこの前、高所作業車で使われているのをたまたま目撃して写真を撮りましたよ」と根本社長は苦笑する。
時計、自動車、産業用ロボットなど、動く機械にはモーターと歯車が欠かせない。モーターによって動力を供給された歯車(ギヤ)は減速させることによって必要な回転速度をもたらす。歯車は動かす荷重に応じて小型歯車、中型歯車、大型歯車と分類されており、小型歯車は時計や産業機械、中歯車は自動車、大歯車は船舶などに使われている。市場で流通する製品には標準品が使用されることが多いが、中には標準品では対応できない荷重を要する製品も少なからずあり、根本製作所にはメーカーから特注品の依頼が来ることも多いという。
根本製作所は桐生市で1966年に根本社長が創業。当時は第一次オイルショックの頃で仕事が少なく、地元モーターメーカーの社長を務めていた根本社長の父からの依頼で歯車の部品加工を行っていた。その後、多様な要請に応じるうちに筺体の製作や組付作業まで行うようになり、加工のための設備も徐々に増やしていったという。多岐に及ぶ設備を保有するため試作機の製作もでき、特注品にも応じられるのはこうした経緯による。さらに、同社の強みは設計から組立まで自社で行っていることだ。
「私どもは設計して製造し、最後の組付までやります。だからこそ一定のクオリティを保てますし、完成までワンストップでできる工場は少ないので、それが強みですね」と自社の強みを説明するのは、父親の根本社長とともに会社を支える根本弘明専務取締役だ。
原材料費高騰でも値下げを迫られ、設計料すらもらえないことも多い。多岐にわたる設備を生かし、企画段階から関わりたい
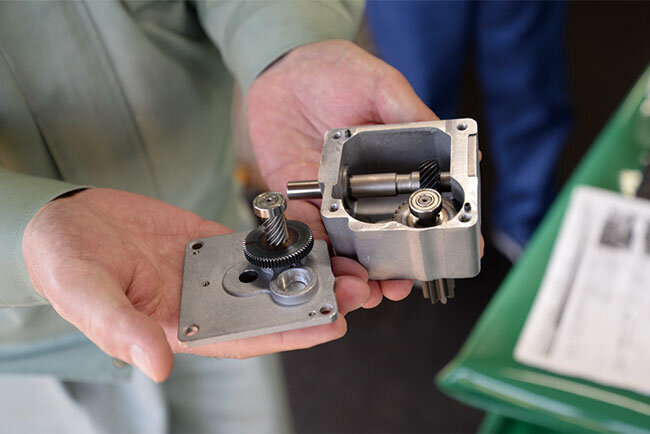
そんな同社の悩みは「コスト」だ。依頼先のメーカーから「もっと安く」と常に迫られるのが悩みの種なのだ。原材料費は高騰しており、国内で海外製品の価格と同等にするのは不可能だ。しかも、特注品は設計にも手間と時間を要する。にもかかわらず設計料すらもらえないことも多いという。
「設計段階で強度計算をせず、標準品を使うケースも多いのですが、コストを下げるため焼き入れをしていないことが多く、劣化が早いです。海外製品を分解してみたことがありますが、やはり焼き入れをしていないものが多いですね」と根本社長は指摘する。以前大手メーカーから、工場の変電所で使われる漏電遮断機の見積りを受けたことがあり、当初は価格が折り合わず海外での生産になった。ところが、出来上がってみると強度不足で使い物にならず、結局根本製作所が月産1,000台の生産を手がけることになったという。「かれこれ30年は故障もなく動いています。工場のような施設の設備は、30年はもつように作ることが必要です」と断言する。さらに根本専務も「SDGsが叫ばれる今、故障しにくく長年使える製品が求められています。長持ちするものづくりは当社の付加価値でもあります」と胸を張る。
しかし、「より安く」と迫られてビジネスチャンスを失う状況から何としてでも脱し、開発段階からメーカーと共同で取り組みたいと根本専務は考えていた。そして、「そのためには新たな生産体制の構築が必要です」とDXによる現状突破を視野に入れている。
AIカメラを備えた検査機器を導入し、時間を要する検査工程を短縮・省力化して人的リソースを組立にまわす計画
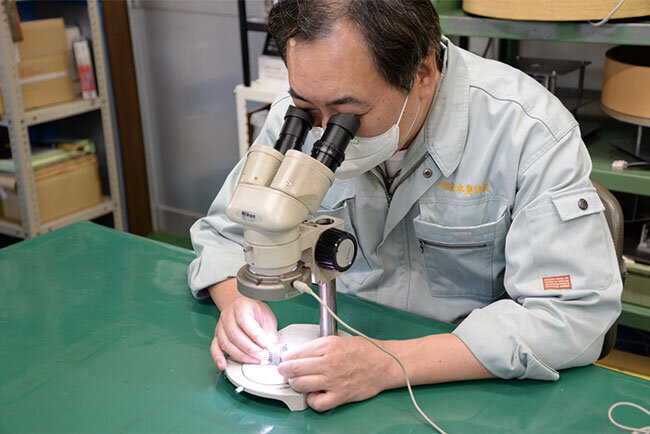
根本専務が現状で課題に挙げていることはいくつかある。一つ目は歯車の検品に要する時間の短縮と省力化、二つ目は設計作業の効率化、そして三つ目が生産管理システムの構築だ。
歯車の検品については、現状では機器による計測と顕微鏡による目視検査を実施している。歯車の間には肉眼では見えないほどの極小の傷があっても駆動時に円滑な噛み合わせができなくなるため、この検査工程はとても重要だ。「組み立てた後に回してみます。その時、歯の中にほんのちょっとでも傷があると異音がしてスムーズに回らない。するとまたばらして歯車を研磨機で磨き直しです」と話す根本社長。しかし、現在は一人の作業者がひと歯ずつ見ているため、1個の部品につき15〜20分程度の時間を要しているという。現在は5~6種類の製品を月産200~300台生産している同社。完成品の部品点数は一台あたりおよそ40個とかなりの数量のため、多くの時間をこの検査に割いている。そこで同社が取り入れようとしているのが、AI機能のついたカメラを備えた画像検査機器だ。この機器を使えば部品1個あたり3~5秒で自動選別できるため、かなりの時間短縮が可能となる。そして、検査で浮いた人的リソースを組立作業に回したいと根本専務は考えている。
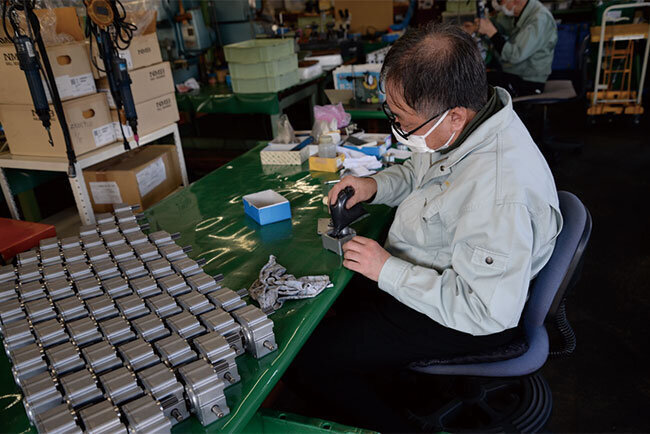
「組み合わせた時の品質を高めるには、人間の熟練した技術が必要です。ここだけは人間がやらないとだめなんです」と断言する根本専務。根本社長も「ロボットでも組立はできます。でも、ちゃんと回転しないんです。スムーズに回転しなければ製品として使い物になりません。だからこそ、どうしても人間の手による組立工程が必要なのです」と続ける。FA(ファクトリーオートメーション)化が進む製造業だが、人間にしかできない工程も確実に存在するのだ。
3D-CADを導入すれば歯車の噛み合わせがシミュレーションできる。取引先とのデータのやり取りにも円滑に応じたい
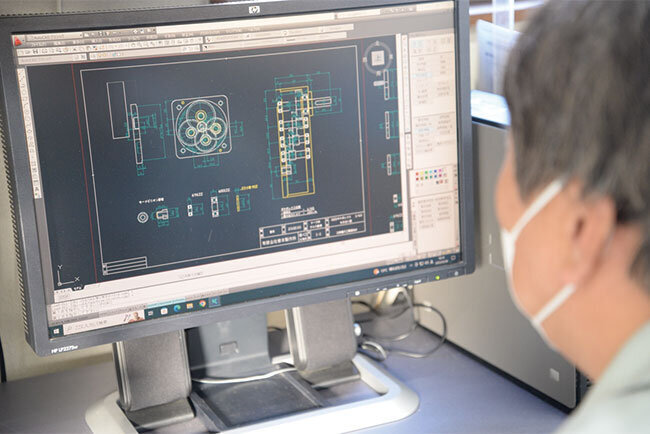
次に、設計作業の効率化という課題に対しては3D-CAD(三次元CAD)の導入によって対応したいと根本専務は考えている。現状で使用しているのは二次元CADのため、パーツの噛み合わせを三面図で確認している。しかし、3D-CADであれば筺体に収まる三次元の立体図で確認をすることができ、設計効率が格段に上がる。さらに、大手メーカーの多くは3D-CADを導入しているため、同じ環境下で図面のやりとりをスムーズに行うことができ、データの劣化も避けられるという。そして、ゆくゆくはこのデータを事務所と工場でリアルタイムに共有できるようにしたいと根本専務は考えている。それは、三つ目の課題である生産管理システムの構築へとつながる。
生産設備のIoT化を実現すれば設計データが迅速に反映できる。事務所と工場で社員が情報共有できる生産管理体制の構築へ
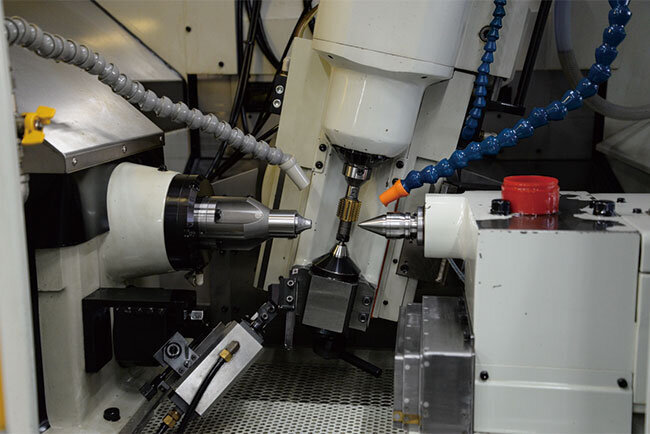
生産管理体制の構築という課題に対して、根本製作所では設備のIoT化を目標に掲げる。現在すでに無線LANは導入されており、IoT化の基盤は整備されている。先述したように、設計図面のデータを事務所から工場に送り、リアルタイムで共有できれば生産効率が上がり、コストダウンにもつながるだろう。さらに、生産の進捗状況を全社員で共有することも生産管理上必要だ。
「今は私が現場でホワイトボードに製品の名称や納期、加工台数を手書きで記入していますが、IoT化を実現すれば、作業者全員が現状把握をしやすくなります」と根本専務は期待を寄せる。現状では工程表をエクセルで作成しているが、こうしたデータも共有したいという。さらに、同社では全員が設計から出荷までの全工程に携わっているため、「工程の見える化」が実現すれば自分の手がける作業の意味が把握しやすく、スキルアップにもつながると考えている。大手メーカーとの取引においても、今後工程の見える化や数値化は必須となるだろう。今や事業規模を問わず、高品質な製品を安定供給することがメーカーの社会的責務として求められている。
大手にはできないものづくり技術で貢献し、新たな付加価値を創出。人間にしかできない部分を生かしてDXへつなげていく
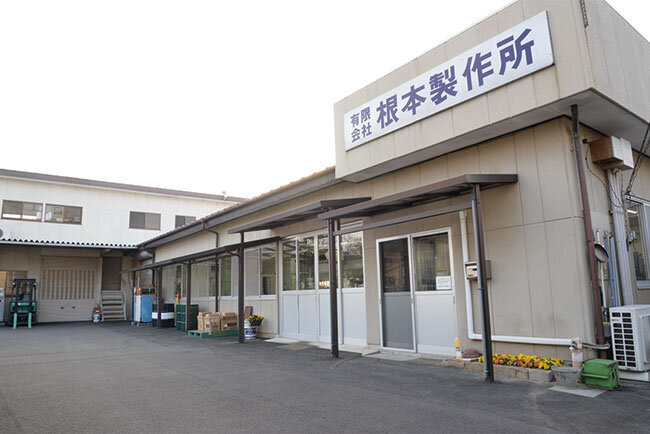
今後の目標を尋ねると根本専務は「ICTを活用した生産体制を基盤に、大手企業との共同開発ができる体制づくりを目指したい。また、人間にしかできないところを大切にしてICTの導入を進めていきたい」と意気込みを語る。そして、根本社長は「他と差別化できるものを国内の取引先と開発したい」と意欲的だ。現状の設備では小ロット対応となり、価格が高くなるのが現実だ。量産にも対応はできない。しかし、「当社には多岐にわたる機械設備がありますので、開発段階から関われれば量産試作まではできます。それに開発料・設計料といった知的財産料を得ることも可能なはずです」と自社の強みを見据えている。幸い、同社はホームページをリニューアルして以来、北は北海道、南は沖縄県まで全国からの問い合わせが増えているという。それは、根本製作所のような仕事ができる製造業が数少ないことの証だろう。
多品種少量生産による技術力を生かして、さまざまな織物製品に活路を求め、貪欲に生き残ってきた桐生の織物生産業。そして、求めに応じて製造工程の範囲を広げ、設備投資も進めてきた根本製作所。両者に共通するのは、高度な技術力と時代の要請への対応力だ。まさに、これからは多様化への対応とたゆまぬ技術研鑽(けんさん)を続けた者のみが生き残っていけるといえるだろう。製造業のグローバル化は止まらず、後継者不足も相まってかつてのような産地形成は国内では難しいかもしれない。けれど、日本に存在する無数の中小製造業が、日本のものづくりの土台を支えていることは紛れもない事実だ。そんな企業がIoTとICTによってタイムリーで正確なものづくりにより新たな付加価値を創造できる。そうすれば、今まで手掛けていないやり方や分野への挑戦も容易になり、DX(デジタルによるビジネスモデルの変革)を実現できれば、日本のもの作りは新たな局面を迎えることになるだろう。根本製作所の今後の挑戦に大いに期待したい。
企業概要
法人名 | 有限会社根本製作所 |
---|---|
所在地 | 群馬県桐生市相生町3丁目532-12 |
電話 | 0277-53-0370 |
HP | https://nemoto-factory.co.jp/ |
設立 | 1966年8月 |
従業員数 | 11人 |
事業内容 | 小型歯車減速機 設計・製造・組立 |