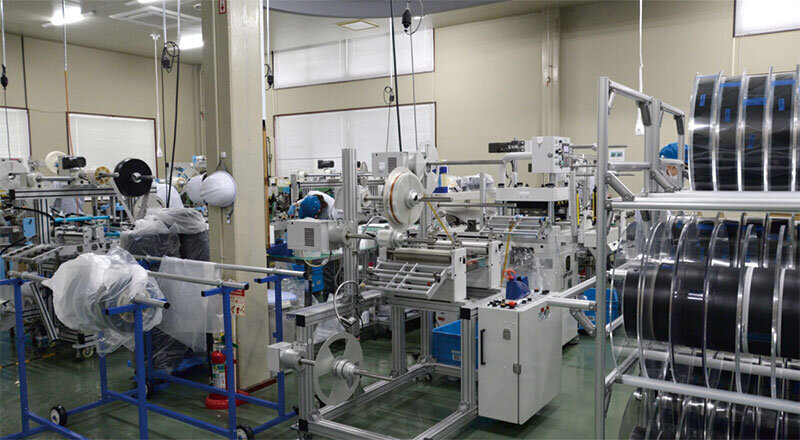
目次
産経ニュース エディトリアルチーム
戦後、ものづくり大国として高い技術と生産力で経済大国へと歩みを進めてきた日本。円高を背景に多くの企業が海外に生産拠点を移した時期もあったが、新型コロナウイルス感染症の世界的な流行や、ウクライナ侵攻によるグローバルサプライチェーンの混乱という危機的な経験を経て、生産拠点を国内に回帰する動きも進む。
2022年9月30日に総務省より公表された「令和3年経済センサス-活動調査」の製造業に関する調査結果では、日本における製造業の2021年の製造品出荷額は302兆33億円、純付加価値額は96兆円超に及び、製造業は日本のGDPのおよそ2割を占める重要な産業となっている。とりわけ中国、アメリカに次いで世界第3位の生産台数を誇る自動車産業は、日本の製造業をリードする重要な産業といえるだろう。
しかしながら、日本においては人口減少による人材不足と技術者の大量退職に対し、今後人員の増強は困難であると予想されている。そこで、大手メーカーでは打開策としてICTの導入を図り、安定的な生産体制の構築を進めている。当然ながら、こうした生産体制の構築は大手メーカーへのサプライヤーである部品メーカーにも求められているが、課題となっているのが、ICTを活用した生産システムの構築に要するコストの問題だ。
福島県郡山市で車載・電気・電子部品の加工業を営む新亜精密株式会社では、2021年から生産管理におけるICT導入を進め、生産効率の向上・売上ともに目覚ましい成果を上げている。莫大な投資額となる生産管理システムの構築に二の足を踏む中小企業が多い中、同社はいかにして導入し、そのコストに見合う成果を得られたのか。その経緯を紹介する。(TOP写真:設計から加工、納品まで社内一貫生産を行う新亜精密の工場。主に車載・電気・電子部品等の加工を手がけている)
人口減少と技術者の人材不足に備え、「誰がやっても生産できる工場」を目指したい
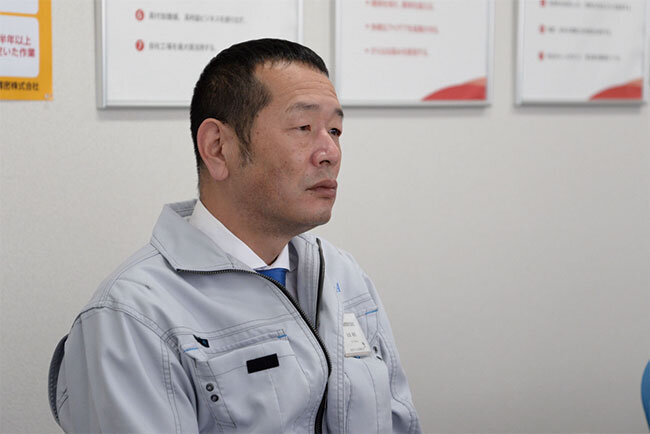
福島県郡山市に本社・製造工場を置く新亜精密株式会社は、関連会社の東亜電気工業株式会社と新成加工株式会社の出資により2004年に設立。精密部品の加工を手がけ、衝突安全関連部品やバッテリー等の車載関連部品を筆頭に、エアコンやスマートフォンなどに使われる電気・電子部品の設計から加工まで、社内一貫生産体制で行っている。また、放熱・断熱用のテープやフィルムといった特殊素材の加工においても高い技術力を誇り、多岐にわたる材料の在庫を有することから短納期での納品にも応じている。
同社がとりわけ強みとしているのが車載関連部品で、生産量は全体の6割を占める。2019年に大手自動車メーカーとの取引が始まって以来、三期連続で増収・増益を果たすほど堅調だ。しかし、少子高齢化と人口減少が進む社会状況において、人材不足は避け難い壁だった。受注は増えているのに限られた人員で対応しなければならないため、同社は設備の稼働力により安定的な製造を目指していた。しかし、度重なる生産遅延が生じる設備の運用システムに問題が生じていた。
それからまもなく、関連会社の新成加工に在籍していた丸田裕司氏が新亜精密の代表取締役に就任したのは2021年のことだ。「当社は技術力に強みがありますが属人化は避け、誰がやっても安定的な生産が可能な工場を目指しています」と話す丸田社長。就任後は工場のレイアウト変更やICT導入を経営方針に掲げ、生産管理体制の刷新に向けて舵を切った。
かつては担当者が紙の伝票で受注管理。生産の進捗が共有できず、納期遅延の原因となっていた
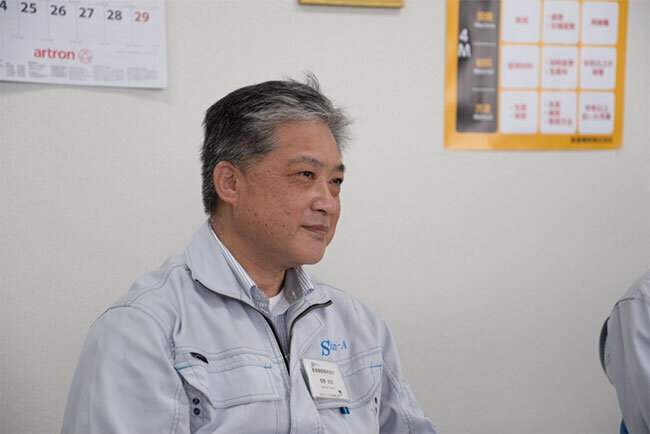
生産効率を高めるために欠かせないのが、在庫や生産進捗の見える化と情報の共有化だ。しかし、新亜精密では創業当初からの旧態依然のやり方から抜け出せないでいた。特に、生産管理が全て紙ベースで行われていたことは大きなネックだった。「月におよそ500〜700件もの受注がありますが、その時に受注した担当者だけが紙の伝票で管理していたので、他の社員にはその内容が把握できていませんでした。しかも、確認しようとするとその人の手を止めてしまうので、時間的なロスにもつながります」と、品質保証課・環境調査室の菅野克志次長は、ICT導入以前の状況を振り返る。
さらに、生産進捗の管理においても課題があった。以前はエクセルで作成した工程表を用いていたが情報量が膨大で、工程表を読み慣れた熟練者でなければ進捗状況の把握は容易ではなかった。「結果的にリアルタイムの生産状況が共有できず、納期の遅れが多発していました」と話す菅野次長は属人化された作業の弊害を痛感していた。しかし、車載部品の受注が始まったことでこの状況を変える必要に迫られた。
「技術だけでは生き残れない」。リアルタイムで生産状況を把握できる仕組みの構築へシフト
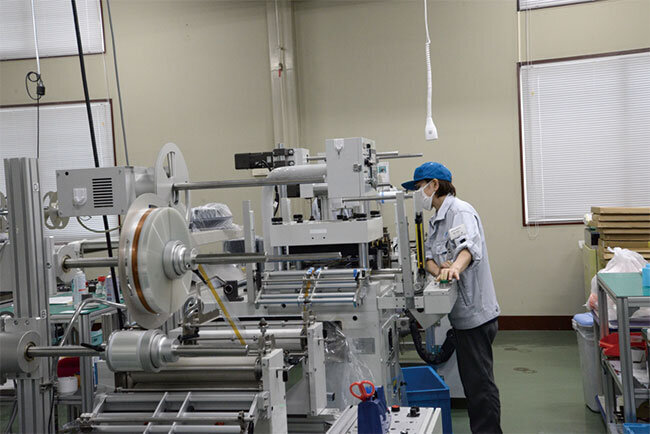
この状況を変える大きな転機となったのが、トヨタなど大手自動車メーカーから求められたIATF16949という国際規格だった。この規格は自動車産業に特化したマネジメントシステムで、サプライチェーンにおける製品の不具合の予防やばらつき・ムダの低減を実現し、高品質な製品の提供を目指す自動車部品のグローバルな調達基準である。そして、新亜精密も車載関係部品の取引が始まるとともに、この規格に準拠した生産工程の数値化や見える化が求められたのだ。
「技術だけでは生き残れない」。そう感じ取った丸田社長は社長就任直後に大号令をかけ、ICTを活用した仕組み作りに早急に取り組むことにした。しかし、莫大な経費はかけられない。同社は積年のネックとなっていた経費の問題をどうクリアしたのだろうか。
オーダーメイドのバーコード生産管理システムを導入し、受注〜生産〜納品状況の把握が容易に
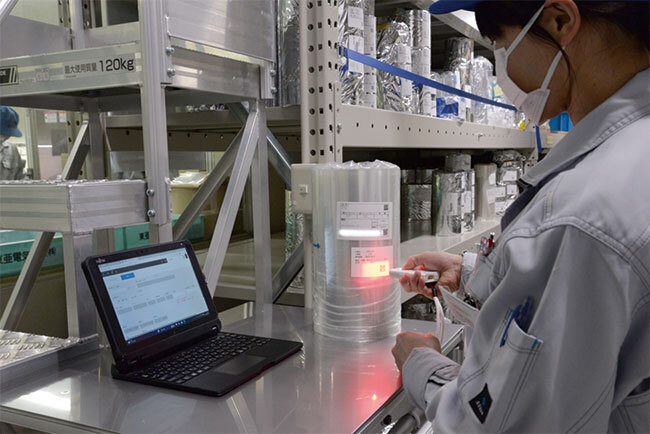
同社が選んだのは業務アプリ構築クラウドサービスだった。このサービスはプログラミングが不要で、自社に合った業務システム(アプリ)を複数選んで構築できる。導入コストも格段に安価だったことも決め手となった。新亜精密ではオーダーメイドによる独自アプリをシステム支援会社に作成依頼し、発注から払い出しまでを一元的に管理する「バーコード管理システム」を2021年3月に導入。
次いで同年12月には「製造工程管理システム」を導入し、生産進捗がリアルタイムで把握できるようになった。さらに翌2022年5月に「設備予約システム」を導入すると、工場のどの設備が使用できるかが一目瞭然となり、生産工程の見通しが立てやすくなったという。
「通常のシステム構築にはスキルのある担当者が必要ですし、構築には数千万の経費がかかります。でも、これらのシステムは100万円単位で導入できるので低コストで済みます。パソコンに不慣れな人にも使いやすいインターフェースも得点が高いですね」と話す菅野次長。同時期に無線LANも設置したことにより、社内のどこからでも端末を介して情報が確認できるようになった。
なお、「製造工程管理システム」導入に先駆け、同社はこれまで使用していたホワイトボードに代えて無線LANでデータ連携ができるIWB(電子ホワイトボード)を導入。それまでホワイトボードに記入していた生産工程表をIWBに移行した。これは生産進捗管理の最初のステップとして、電子化を目的に導入されたものだった。その後は業務管理クラウドサービスで一元管理するようになり、現在IWBは会議や社内サイネージとしての役目を果たしている。
「誰がやっても安定的な生産が可能な工場」を目指すという丸田社長の言葉通り、この2年間でICTの導入を果たした結果、熟練の作業者でなくてもパッと見て生産状況がわかるようになり、現場からは「どこに負荷がかかっているかも把握しやすくなった」「管理が楽になった」「段取りをつけやすくなった」という声が聞かれるようになったという。
人員を増やしていないのに遅延がゼロに。売上も1.5倍以上へ
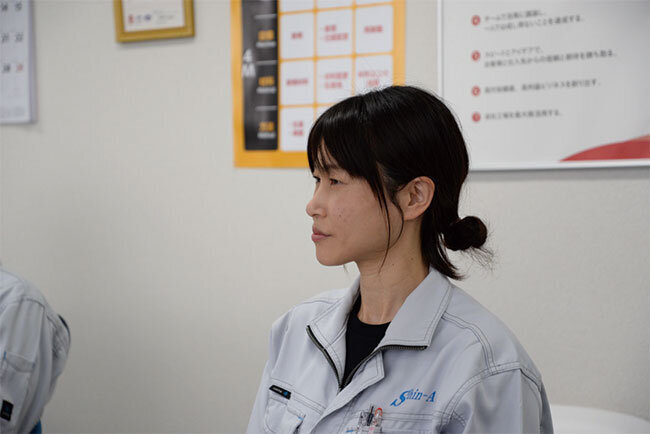
ICT導入の成果は、数字にもはっきり表れた。人員を増やしていないにもかかわらず、生産の遅延がゼロになったのだ。「3年前は1ヶ月に約20件もの生産遅延があったのですが、今はゼロになりました。生産状況がリアルタイムでわかるようになったので、対策を立てられることが大きいですね」と話す菅野次長。その言葉通り、遅延の恐れがある案件に対し自動でフラグが立つため、遅れを見つけにいかずに済むのもかなり効果的だった。現在は1週間のリードタイムを設けているため、進捗状況が把握できれば遅れが出ても取り戻せるという。
さらに、生産効率が向上したことで売上も上がり、ICT導入以前には月間5~6千万円だった売上が、現在では9千万円まで増えている。
社員の働き方にも変化が見られた。進捗状況が把握できることで精神的なストレスが軽減し、見通しが立つことにより安心感も得られるという声も上がっている。さらに、効率的な生産体制が実現したことで残業が20%減少するという相乗効果もあった。
システムの立ち上げに従事した業務課の渡邉知恵子さんは「1から仕組みが出来上がっていくのを見て、やりがいを感じました。それに、普段あまり声を上げない社員からも『システムを導入して良くなった』という声を聞くようになりました」と手応えを感じている。
今後は保有設備全てにおいてIoT化を進めていく
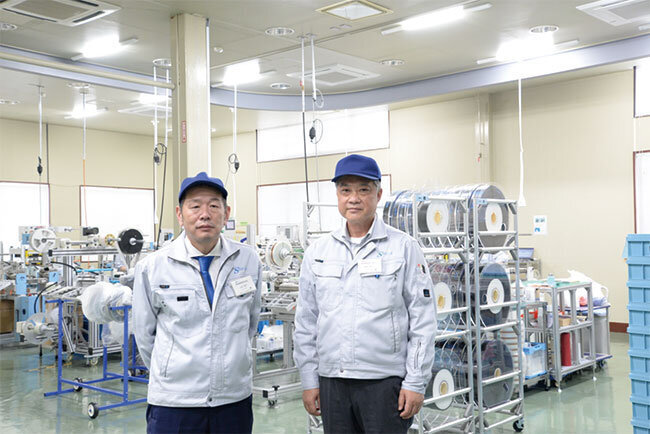
積年の課題から脱し、効率的な生産システムの構築を果たした新亜精密。丸田社長に今後の目標を尋ねると、「生産システム作りにゴールはありません。現在プレス機のIoTを計画中ですが、いずれは保有するすべての設備のIoT化を進めたいと思っています」と意欲的だ。社内では無線LANによって社屋・工場のどこからでも情報が共有できるため、すべての生産設備同士もネットワークで結べば、さらに効率的な生産が可能となるだろう。
なお、同社はインボイス制度に備え、2022年に経理ソフトも新たに導入している。これまではエクセルに手入力だったため、入力ミスのリスクがあったが、新たなソフトは生産システムと連動しており、経理処理がスムーズに運ぶようになった。
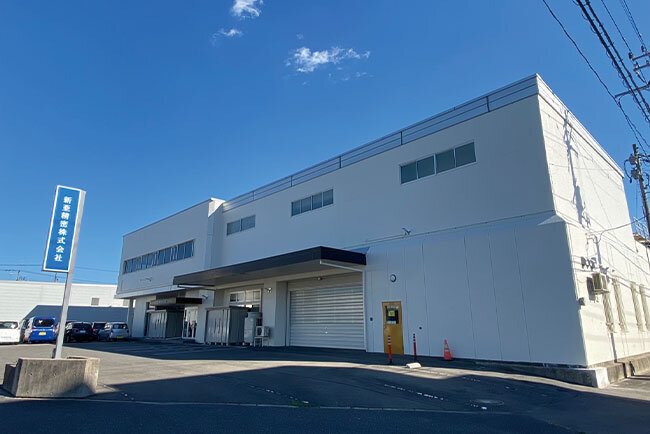
「中小規模の製造業におけるICT導入はまだまだ遅れている」と話す丸田社長。それは日本の中小企業が共通して抱える悩みでもある。しかし、だからこそ自分たちのように小さな事業規模の会社で大きな売上を達成できることに、大きな価値を感じているという。
「福島県は人口が減っていますし、都会より給料も安い。ただ、土地は安くても物価は都会と変わらないんです。だからこそ生産効率を上げて利益を増やし、社員の給料を増やすことが重要なんです」と語る。丸田社長にとって社員はその家族も含め、「我が子のような存在」だという。きっと他の中小企業の経営者たちも同じ思いを抱いているはずだ。そんな経営者たちと同様の悩みと長年向き合ってきた同社だからこそ、その行動力と躍進は日本中の中小製造業の希望となるだろう。
企業概要
法人名 | 新亜精密株式会社 |
---|---|
所在地 | 福島県郡山市喜久田町卸1丁目106番1号 |
電話 | 024-963-1666 |
HP | https://shinaseimitsu.com/ |
設立 | 2004年10月 |
従業員数 | 46名 |
事業内容 | 電気部品・電子部品・車載部品の製造・販売 |